Klaus A/C Tower KAC Series
Dust collector for adsorption tower
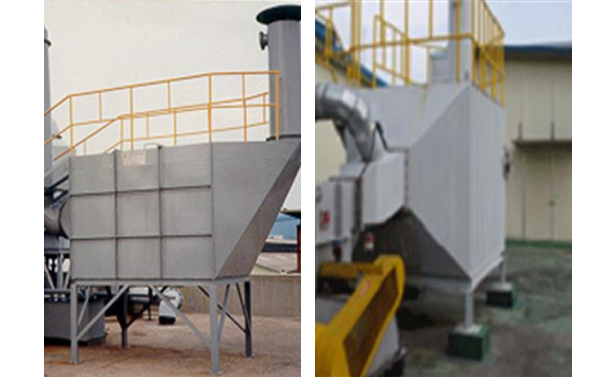
Purpose of use
Adsorption Tower (A/C Tower)
Active Carbon
- Activated carbon is a collection of amorphous carbon with well-developed micropores made from wood, lignite, anthracite and palm bark, and is an adsorbent that has a large internal surface area due to well-formed micropores about the size of molecules during activation.
- Activated carbon has a surface area of more than 1,000 m2 per unit g, and the functional group of carbon atoms on the surface has the property of adsorbing adsorbed molecules by exerting attraction on the surrounding liquid or gas.
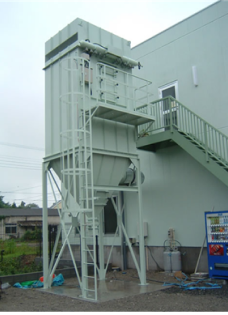
Types and uses of adsorbents
scroll left and right >
Adsorbent | Purpose |
---|---|
Active carbon | Solvent recovery, odor removal, gas purification (most common) |
Alumina | Drying of gases, air and liquids |
Bauxite | Removal of oil from petroleum, drying of gases and solutions |
Bone char | Decolourization of sugar |
Decolorizing carbon | Removal of oil, pigments, oil and wax, bleaching of beverages |
Fuller's earth | Refining of lubricants, fats and waxes |
Magnesia | Refining of petrol and solvents |
Silica gel | Removal of impurities from sodium hydroxide solution |
Strontium sulfate | Drying and purification of gas; removal of iron from sodium hydroxide solution |
Adsorption by an adsorbent such as activated carbon
- At the same flue gas temperature, the amount of harmful gas adsorbed on adsorbents such as activated carbon increases with increasing molecular weight.
- Substances that are liquid at room temperature and those with a boiling point close to room temperature are often advantageous for the adsorption method.
Types and uses of adsorbents
scroll left and right >
Gas | Activated carbon for acid gas | Activated carbon for basic gas | ctivated carbon for neutral gas |
---|---|---|---|
Benzene | |||
Toluene | |||
Xylene | |||
Stielt | |||
Carbon disulfide | |||
Thiophene | |||
Acetone | |||
Acetic acid | |||
Hydrogen sulfide | |||
Methanethiol | |||
Methyl sulfide | |||
Methyl disulfide | |||
Trimethylamine | |||
Monomethylamine | |||
Ammonia |
Physical adsorption
chemical adsorption
Features
Turbo fan
- Aluminum alloy is used to reduce the idle weight and start up load, thus increasing the absorbing force, and electronic balancing with the mould has achieved zero vibration and low noise.
- Eliminates vibration caused by dirt squeezed between or stuck to the fan blades during use.
Coating
- Maximized durability and luxury with a high quality coating
- Coated with chemical resistant material
Maintenance
Dust inflow
- Pay attention to the inflow of dust that closes the surface of the adsorbent during operation.
- The inflow of dust reduces the surface area of the adsorbent and closes the fine capillary tube in the adsorbent, so that the adsorption efficiency is very low. Therefore, to solve this problem, a dust removal filter must be installed at the adsorption stage.
Corrosion
- The material is corroded by steam during desorption stripping. As the water vapour temperature increases, corrosion also increases relatively, so the material must be made of stainless steel or a special surface treatment must be carried out to prevent corrosion.
Polar and non-polar compounds
- Activated carbon can adsorb both polar and non-polar substances, but additional separation methods such as distillation are required to recover polar substances desorbed by water vapour during desorption stripping.
Design Condition
Category | Range |
---|---|
Filter rate (m/sec) | 0.1 ~ 0.5 |
Inflow rate (m/sec) | Under 18 |
Contact rate (sec) | Over 1.0 |
Adsorbent Size (mesh) | 4 ~ 8 |
Thickness of the filling layer (cm) | Over 35 |
Pressure loss (mmAq) | Under 150 |
Charging density (g/L) | 350 ~ 950 |
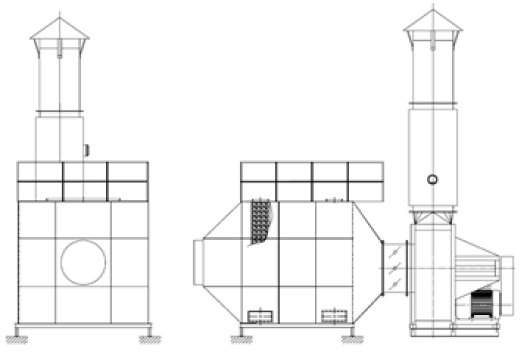